The common coil design is a 2-in-1 conductor-friendly block coil design based on simpler ends with large bend radii (see Fig. 1). Unlike in most designs, where the bend radii are determined by the aperture, in a common coil dipole, the bend radii are determined by the separation between the two apertures which is much larger than the aperture. The common coil design easily accommodates high field, brittle conductors or those cables that require large bend radii. The large bend radii in the common coil geometry allows both “Wind & React” and “React & Wind” technologies. In several ways, the common coil design may be a technically superior solution for high field magnets because the coils are primarily stacked vertically and move as a unit against the large horizontal Lorentz forces. This largely eliminates the internal strain on the conductor at or near the end region of the superconducting coils when the two sides of the coil move apart under Lorentz forces – a very different situation as compared to that in the conventional block coil or cosine theta dipole designs (see Fig. 3 below). As compared to the conventional block coil designs, the common coil block coil design eliminates almost all of the hard-way bends (or ends requiring long length). The only remaining hard-way bends are in the small pole coils (see, for example, Figure 2), and some designs (such as overpass/underpass or cloverleaf) practically eliminate the hard-way bends in those as well.
- Also see The DCC017 Story
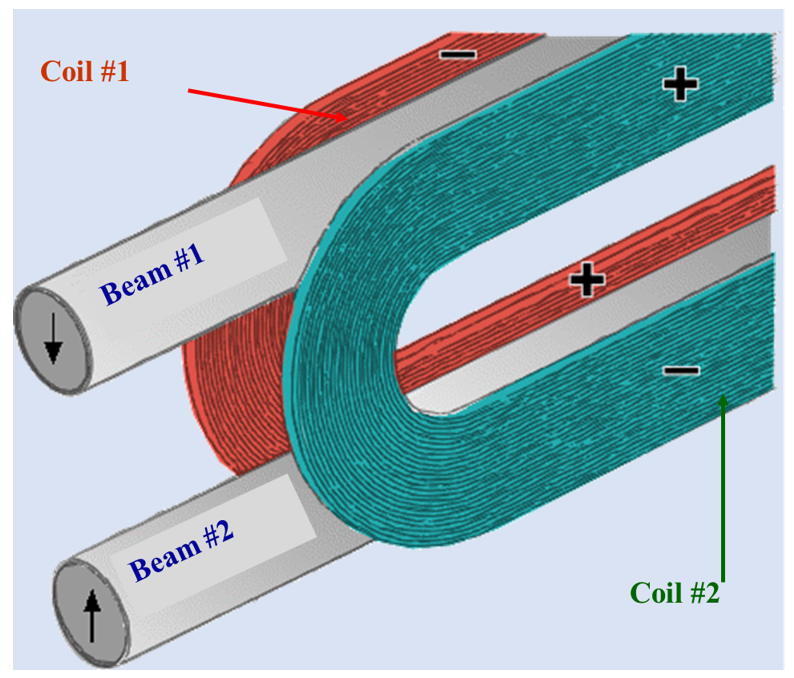
Fig. 1: Main coils of the common coil design
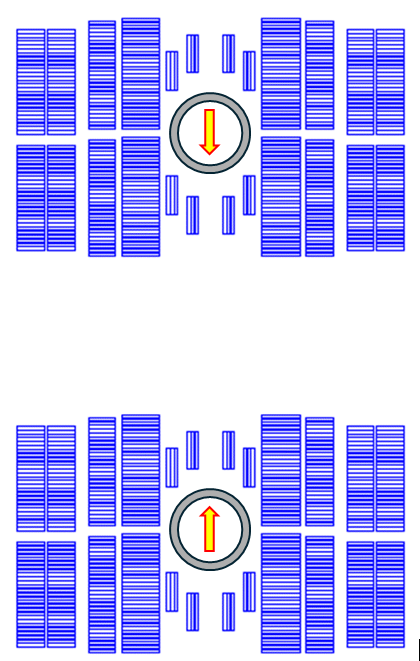
Fig. 2: Accelerator quality common coil design with the main coils (horizontally oriented) with the pole coils (vertically oriented) providing the field quality.
The common coil design facilitates a modular geometry that is particularly attractive for hybrid magnet designs using both High Temperature Superconductors (HTS) and Low Temperature Superconductors. The common coil design also offers easier vertical segmentation which is ideally suitable for hybrid designs. Such magnets use coil modules made with different conductors (Nb3Sn, NbTi and HTS). The segmentation between HTS and LTS is efficient in common coil dipole and it provides natural and easier stress management. These features are applicable for both R&D magnets and for large-scale production magnets.
In addition to allowing versatility in conductors and technologies, the common coil design is also one of the most likely candidates for providing lower cost, and more reliable large scale production of high field 2-in-1 collider dipoles with a good technical performance since (a) simpler racetrack coils requires simpler tooling; (b) half the number of coils required as the coils are shared between two apertures, and (c) geometry requires less structural material since the coil modules can be allowed to move as a whole.
In the common coil design, large horizontal Lorentz forces associated with the high field accelerator magnets would cause much smaller internal strain in the conductor or coil since the coils move as a unit (Fig. 3, right) as compared to that in the Cosine Theta (CT) or the Canted Cosine Theta (CCT) or the block coil designs where such movements would cause a large internal strain at or near the end region (Fig. 3, left).
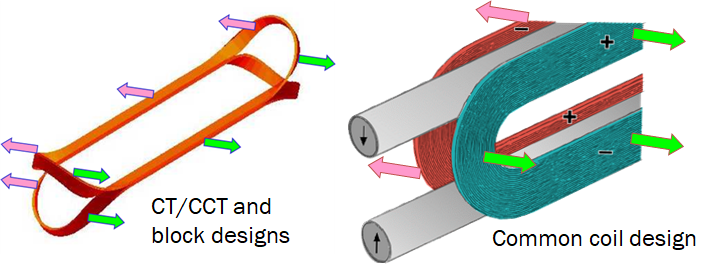
Fig. 3. Pictorial representation of the Lorentz forces (a) in the cosine theta, canted cosine theta and block design versus (b) in the common coil design.
The common coil design was considered for the main dipoles of the very large hadron collider (vlhc) proposal in US and is being considered for the proposed Super proton-proton Collider (SppC) in China and for the proposed Future Circular Collider (FCC) and/or HE-LHC at CERN.
- See publications on the common coil design (first paper, internal note)
- See presentations on the common coil design (seminar at CERN)
- Design studies under US Magnet Development Program (status March 2022)
In summary, some of the benefits of the common coil geometry are:
- Simple 2-d coil geometry for collider dipoles
- Conductor friendly design with large bend radii (determined by the spacing between the two apertures rather than the magnet aperture itself) allowing a variety of conductor/cable options (e.g., cables being developed for fusion)
- Efficient segmentation between HTS and LTS coils in HTS/LTS hybrid dipoles
- Allows aperture to be changed for “higher field, smaller aperture”, or “lower field, larger aperture” with the same coil for magnet R&D
- Mechanically handles well the large Lorentz forces associated with the high fields, creating lower internal strain on the conductor despite large deflections
- Fewer coils (half) because the same coils are shared between two apertures
- Simpler magnet geometry and simpler tooling should lead to increased reliability and reduced manufacturing costs
- Allows both “React & Wind” and “Wind & React” options
- Allows more technology options for insulation, etc., as they don’t have to go through the high temperature reaction cycle
- Allows rapid-turn-around, low-cost R&D for systematic and innovative studies, as demonstrated with the Common Coil Test Facility (CCTF) at the Brookhaven National Laboratory